On the progress side, I painted the slots and grooves on the booster cover bodies. My MDF mask didn't work out quite as well as I had hoped, I probably would have been better off using masking tape, or a combination of the two (which I did toward the end).
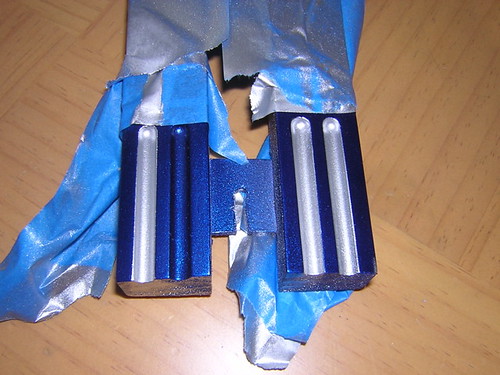
On the setback front, when I painted the booster cover tops, I kind of messed up the paint job in the slots. So I tried to repair that tonight, and ended up ruining the whole paint job on the booster cover tops. I need to repaint them. I may even repaint the booster cover bodies while I'm at it, I haven't decided. Most of a week's worth of prep down the drain. :(
Back to progress, I trimmed the styrene channel in the slot in each ankle.
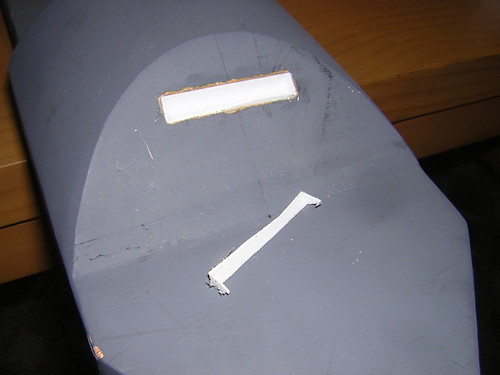
Later, I filled gaps with putty and sanded. That turned out okay.
I finished up by using silicone to place the shoulder hub details into the hubs, and applied some primer to resin parts (ankle cylinder wedges, ankle details).