R2 took his first steps today. Here's the tale of how the day went.
I got to Mike's around 10:00am, William Miyamoto joined us a short time later, and Roy Powers also dropped by for a while and lent a hand. My main function was to stay out of the way as much as possible and operate the video camera, as we were shooting the wire-up for a DVD tutorial.
Mike and William worked on wiring up the Saturn motors.

Meanwhile, Roy tinned up some of the data lines for the sound card.

Part of the DVD tutorial included some whiteboard explanation. Mike explained radio control basics, and later diagrammed how the dome motor controller worked.
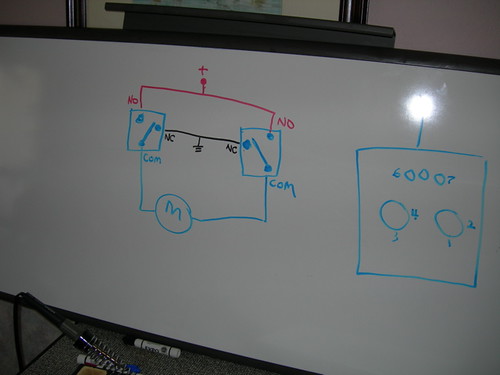
We had a late lunch break (around 2:30pm) and wolfed down pizza before returning to work.

I got into the act every once in a while, mostly hacking aluminum and drilling pieces here and there. I also wired up the data lines for the sound card, and there are a lot of connections to make (32 total, 16 on the Vantec Keycoder, and 16 on the sound card).

Mike added parts to the frame as we went along. The receiver, main receiver battery, and the backup receiver battery were installed, along with the dome motor controller.

Mike and William soldered up battery connectors and other wiring.

The Vantec Keycoder and speed controller were installed and wired up.

After a lot more work, it was finally time to try out R2. We powered up the receiver, main power and transmitter. The first thing I tried was the dome motor. It worked! Well, it worked backward, but it worked. William made some adjustments on the transmitter that reversed the behavior, and fixed things so that the dome motor turned properly. We could have swapped how the wires were connected on the dome motor, but this was easier.

Next, I moved R2 forward. As with the dome motor, we had a connection that wasn't quite right on the speed controller. A quick swap of a connection, and R2 was moving like he should! I was all smiles.

No video to share yet, but I should have some in the next day or two.
The bad news: We blew up the CF Sound III card. We accidentally hooked it up to 24 volts, which is more than it can handle. I'm pretty sure the card is dead. I'll get a replacement some way or another. Oh well. If that's the worst thing that happens, I'll be a happy man.
R2 will spend the night at Mike's house, it was too late to tear him apart and pack him in the car by night's end. I'll pick him up Sunday and bring him home.
Thank you Mike, William, and Roy, for getting R2 that much closer to a dream come true!